Centrifugal pumps are widely recognized for their efficiency in moving large volumes of fluid. They operate on the principle of centrifugal force, where an impeller rotates rapidly, imparting kinetic energy to the fluid. This energy transforms into pressure energy as the fluid is forced out of the pump casing. Centrifugal pumps are typically used in applications that require high flow rates and moderate to high pressure, making them ideal for water supply, irrigation, and industrial processes.
One of the defining features of centrifugal pumps is their volute casing design, which allows for smooth fluid flow and minimal turbulence. This design contributes to their efficiency and helps reduce wear on the pump components. Moreover, centrifugal pump can handle various fluids, including clean water, slurries, and chemicals, depending on the materials used in their construction.
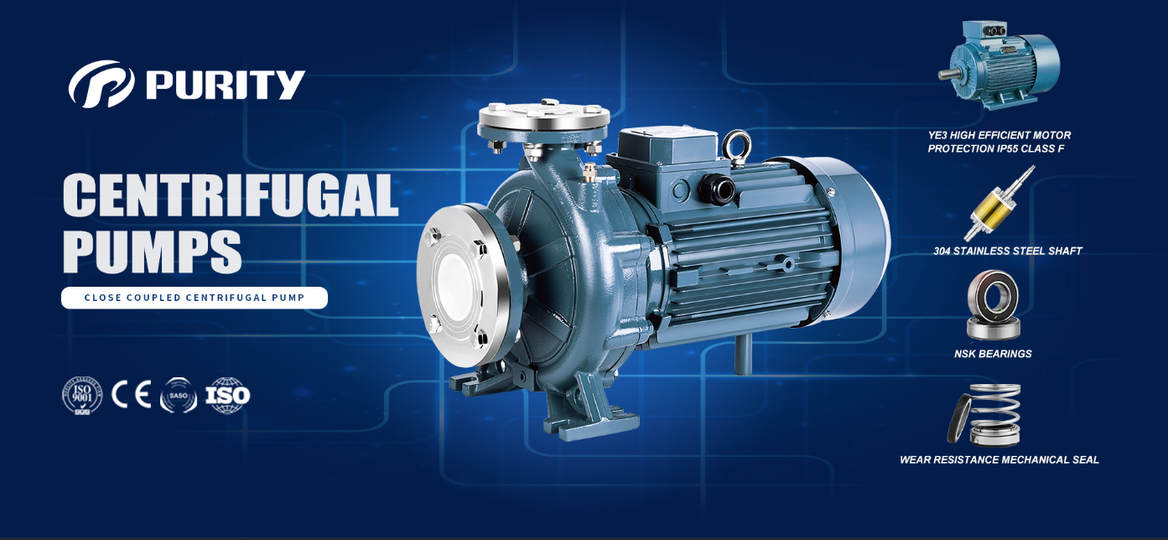
Figure| Purity Centrifugal Pump PST
Introduction of Inline Pump
Inline pumps, are specifically designed for applications where space constraints are a concern. Unlike centrifugal pumps, inline pumps are characterized by their compact design, where the inlet and outlet are aligned along the same axis. This configuration makes them easier to install in tight spaces and enables seamless integration into existing piping systems.
Inline pumps are commonly used in applications that require consistent flow rates, such as HVAC systems, hot water circulation, and fire protection systems. Their design allows for easy maintenance, as the pump can often be removed from the pipeline without having to disconnect the piping. This feature is particularly advantageous in commercial settings where downtime needs to be minimized.
Differences Between Centrifugal Pumps and Inline Pumps
1.Design and Configuration
Centrifugal pumps have a volute casing and are typically mounted horizontally, while inline pumps have a streamlined design with a straight-through flow path, making them easier to install in limited spaces.
2.Flow Characteristics
Centrifugal pumps excel at high flow rates and can handle varying fluid levels, whereas inline pumps maintain consistent flow rates and are better suited for applications with stable fluid demands.
3.Energy Efficiency
Both pump types can be energy-efficient, but centrifugal pumps are generally more efficient at handling larger volumes of fluid. Inline pumps, while efficient in their applications, may have slightly higher energy consumption due to their design constraints.
4.Maintenance
Inline pumps offer more straightforward maintenance due to their design, allowing for easy access and service without disrupting the entire piping system. In contrast, centrifugal irrigation pumps may require more effort to service, particularly if they are part of a larger installation.
Purity Inline Pump Has Unique Advantages
Compared with other water pumps in the same industry, Purity inline pump has the following unique advantages:
1. The whole machine has a compact structure, small and light.
2. The connection and end cover are integrally cast to improve the connection strength and concentricity.
3. F-class enameled wire, equipped with IP55 protection grade motor, has better energy saving effect than ordinary motor.
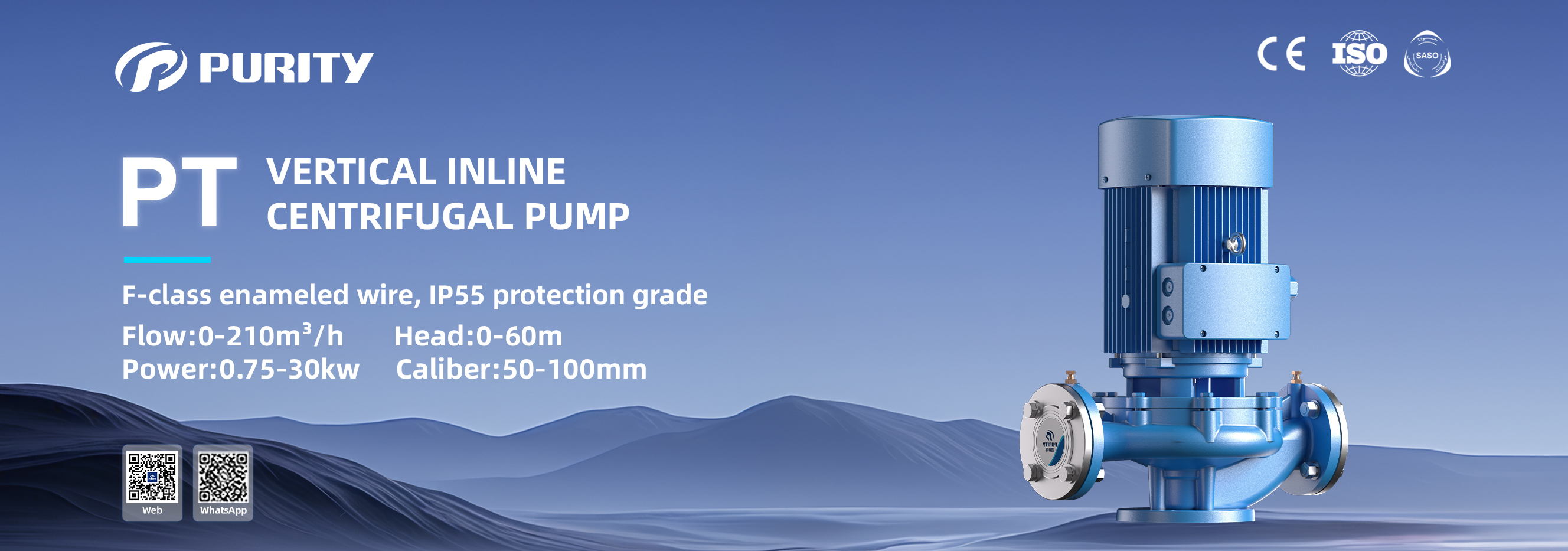
Figure| Purity Inline Pump PT
Summary
Choosing between a centrifugal pump and an inline pump depends on various factors, including space, application requirements, and maintenance considerations. Understanding the differences between these two types of pumps can significantly impact the efficiency and reliability of fluid transport systems. As industries continue to evolve and seek more efficient solutions, both centrifugal and inline pumps will remain integral to modern fluid handling practices.Purity pump has significant advantages among its peers, and we hope to become your first choice. If you are interested, please contact us.